Ein Maschinenbauer erinnert sich: „Früher haben wir unsere Maschinen nach bestem Wissen gebaut und einfach laufen lassen. Es ging jahrelang gut – bis eines Tages doch ein Unfall passierte.“ Solche Geschichten zeigen, warum eine Risikobeurteilung für Maschinen und Anlagen heute unverzichtbar ist. In diesem Blogbeitrag erklären wir, was es mit der Risikobeurteilung auf sich hat, warum sie nach Maschinenrichtlinie gesetzlich vorgeschrieben ist, und wie Unternehmen von einer gründlichen Risikobeurteilung profitieren. Dabei betrachten wir historische Entwicklungen, den aktuellen Stand und zukünftige Trends. Praxisbeispiele, persönliche Anekdoten sowie Vergleiche und Metaphern machen das komplexe Thema leicht verständlich.
Was ist eine Risikobeurteilung und warum ist sie so wichtig?
Eine Risikobeurteilung ist ein systematischer Prozess, bei dem alle möglichen Gefährdungen identifiziert und die damit verbundenen Risiken bewertet und minimiert werden. Ziel ist es, Maschinen so sicher zu gestalten, dass weder im Normalbetrieb noch bei vorhersehbarem Fehlgebrauch Menschen zu Schaden kommen. Kurz gesagt: Risikobeurteilung bedeutet aktive Unfallprävention, von der Planung bis zur Betriebsphase einer Maschine.
Historisch wurde anstelle von „Risikobeurteilung“ oft der Begriff „Gefahrenanalyse“ verwendet. Doch mit der EU-Maschinenrichtlinie 2006/42/EG hat sich nicht nur der Begriff gewandelt – auch der Anspruch ist gestiegen. Moderne Risikobeurteilung betrachtet das Produkt aus Eintrittswahrscheinlichkeit und Schadensschwere eines Ereignisses. Je wahrscheinlicher ein Unfall und je schwerer mögliche Verletzungen, desto größer das Risiko. Durch konstruktive Maßnahmen kann der Entwickler an beiden Stellschrauben drehen: Er senkt die Wahrscheinlichkeit eines Unfalls und mildert potenzielle Folgen.
Ohne Risikobeurteilung kein CE: Für Hersteller von Maschinen ist die Risikobeurteilung nicht optional, sondern gesetzliche Pflicht. Tatsächlich darf ohne vorliegende Risikobeurteilung weder eine EG-Konformitätserklärung ausgestellt noch eine Maschine mit dem CE-Zeichen versehen werden. Mit anderen Worten: Eine nachweisliche Risikobeurteilung ist die Voraussetzung, um eine Maschine in Europa überhaupt in Verkehr zu bringen. Das allein unterstreicht ihre enorme Bedeutung.
Rechtliche Grundlagen: Risikobeurteilung nach Maschinenrichtlinie 2006/42/EG
Die Maschinenrichtlinie 2006/42/EG der EU schreibt vor, dass jeder Maschinenhersteller eine Risikobeurteilung durchführen muss. Wörtlich heißt es: „Der Hersteller einer Maschine […] hat dafür zu sorgen, dass eine Risikobeurteilung vorgenommen wird, um die für die Maschine geltenden Sicherheits- und Gesundheitsschutzanforderungen zu ermitteln. Die Maschine muss dann unter Berücksichtigung der Ergebnisse der Risikobeurteilung konstruiert und gebaut werden.“. In deutsches Recht ist dies durch die 9. Verordnung zum Produktsicherheitsgesetz (Maschinenverordnung) umgesetzt. Eine Risikobeurteilung ist somit gesetzlich vorgeschrieben und keine freiwillige Leistung.
Doch was bedeutet „geltende Sicherheits- und Gesundheitsschutzanforderungen“? Hier kommt die DIN EN ISO 12100 ins Spiel – die zentrale Norm zur Maschinen-Risikobeurteilung. Diese harmonisierte europäische Norm gibt Entwicklern Leitlinien, wie sie unabhängig vom Maschinentyp schrittweise Risiken ermitteln und minimieren können. Sie ersetzt ältere Normen (wie die zurückgezogene EN ISO 14121) und spiegelt den „allgemein anerkannten Stand der Technik“ wider, an dem sich Hersteller orientieren.
Neben der Maschinenrichtlinie selbst existiert ein ganzer Kosmos weiterer Richtlinien und Normen, die je nach Maschine relevant sind – vom elektrischen Sicherheit (Niederspannungsrichtlinie) bis zu spezifischen Maschinentyp-Normen (sogenannte C-Normen, z.B. für Pressen oder Roboter). Rund 500 harmonisierte Normen besitzen eine Vermutungswirkung, was bedeutet, dass ihre Einhaltung zugleich die Anforderungen der Maschinenrichtlinie erfüllt. Ein wichtiger Schritt im Risikobeurteilungs-Prozess ist daher, alle einschlägigen Normen und Vorschriften für die Maschine zu ermitteln.
Welche Maschinen sind betroffen? Grundsätzlich alle Maschinen, die in der EU in Verkehr gebracht werden, müssen eine Risikobeurteilung durchlaufen – vom einfachen Förderband bis zur komplexen Industrieanlage. Auch Eigenbauten in Unternehmen sind eingeschlossen: Wer eine Maschine nur in Losgröße 1 für den Eigenbedarf herstellt, gilt rechtlich als Hersteller und muss ebenfalls eine Risikobeurteilung durchführen. Zudem verlangt die Maschinenrichtlinie eine Betrachtung von Anlagen aus mehreren Maschinen als Gesamtheit (Stichwort „Verkettung von Maschinen“). Wenn also ein Unternehmen einzelne Maschinen zu einer verketteten Anlage kombiniert, entsteht meist eine neue Gesamtmaschine – wiederum mit Pflicht zur Risikobeurteilung dieser Gesamtheit. All dies zeigt: Kein Weg führt an der Risikobeurteilung nach Maschinenrichtlinie vorbei, will man rechtskonform agieren.
Schritte einer Risikobeurteilung in der Praxis
Wie geht man nun konkret vor, um eine Maschine „auf Herz und Nieren“ in puncto Sicherheit zu prüfen? Die Maschinenrichtlinie selbst gibt in Anhang I einen grundsätzlichen Fahrplan vor. Dieser Prozess lässt sich in mehrere Schritte gliedern, die iterativ – also bei Bedarf mehrfach – durchlaufen werden, bis ein akzeptables Restrisiko erreicht ist:
Grundlegende Schritte bei einer Risikobeurteilung sind beispielsweise in DIN EN ISO 12100 beschrieben. Zunächst werden die Grenzen der Maschine festgelegt: Was ist ihr Zweck, wer nutzt sie, wo und wie wird sie betrieben? Dann gilt es, Gefährdungen, Gefährdungssituationen und -ereignisse zu identifizieren – also alle möglichen Gefahrenquellen in jeder Phase des Maschinenlebenszyklus zu finden (von Montage über Betrieb bis Wartung und Entsorgung). Anschließend werden die Risiken abgeschätzt: Wie wahrscheinlich ist das Eintreten jeder Gefahr und wie schlimm wären die Folgen? Daraus ergibt sich eine Risikoeinstufung. Nun folgt die Risikobewertung: Ist dieses Risiko akzeptabel oder nicht? Falls nein, müssen Maßnahmen zur Risikominderung getroffen werden – und dann wird der Zyklus erneut durchlaufen, beginnend wieder bei der Identifikation weiterer Gefährdungen, bis alle Risiken soweit reduziert sind, dass sie vertretbar sind.
In der Praxis hilft oft eine Visualisierung dieses Prozesses, wie in der obigen Grafik dargestellt. Wichtig ist: Die Risikobeurteilung begleitet den gesamten Entwicklungsprozess. Sie startet idealerweise schon bei den ersten Konzepten und läuft parallel zur Konstruktion. Man wartet nicht, bis die Maschine fertig aufgebaut ist – man denkt von Anfang an an die Sicherheit. Dadurch fließen die gewonnenen Erkenntnisse unmittelbar ins Design ein. Eine späte Änderung kurz vor Inbetriebnahme kann teuer und aufwendig sein; eine frühzeitige Erkennung von Risiken hingegen ermöglicht es, Probleme elegant durch Designänderungen zu lösen, bevor überhaupt etwas gebaut ist.
Beispiel: Vom Risiko zur Lösung
Stellen wir uns ein Beispiel vor: Eine Verpackungsmaschine soll Dosen befüllen und verschließen. Bei der Gefährdungsanalyse entdeckt das Team eine potenzielle Gefahr: Beim Wechseln der Dosenformate muss ein Mitarbeiter nahe an bewegliche Teile greifen – Quetschgefahr! Die Risikoeinschätzung ergibt ein unakzeptables Risiko für Handverletzungen. Was tun? Im Rahmen der Risikobeurteilung entwickelt das Team eine Lösung: Ein spezieller Sensor mit Lichtschranke stoppt die Maschine automatisch, sobald jemand in die Gefahrenzone greift. Zusätzlich wird ein mechanischer Schutzbügel angebracht. Nach dieser Änderung wird die Risikoanalyse erneut durchlaufen: Nun ist die Wahrscheinlichkeit einer Verletzung extrem gering. Das Risiko wird als akzeptabel bewertet – Problem erkannt, Gefahr gebannt. Dieses einfache Beispiel zeigt den Kern der Risikobeurteilung: systematisch Gefahren aufdecken und konstruktive Gegenmaßnahmen finden.
Häufige Herausforderungen und Fallstricke
Eine Risikobeurteilung klingt in der Theorie geradlinig, bringt aber in der Praxis einige Herausforderungen mit sich. Die größte Hürde ist oft, wirklich alle Gefährdungen zu erkennen. Maschinen sind komplex, und Gefahren lauern manchmal an unerwarteten Stellen. So müssen auch ungewöhnliche Betriebszustände berücksichtigt werden – etwa ein Wartungstechniker, der Abdeckungen entfernt, oder eine Fehlbedienung, die zwar unwahrscheinlich, aber vorhersehbar ist (z.B. das Umgehen einer Schutzeinrichtung aus Bequemlichkeit). Laut einem Bericht der Bundesanstalt für Arbeitsschutz (BAuA) ist die umfassende Identifizierung aller Gefährdungen über den gesamten Lebenszyklus einer Maschine tatsächlich der schwierigste Teil des Prozesses. Hier helfen Checklisten und Normen: Viele C-Normen (spezielle Maschinentyp-Normen) enthalten Listen typischer Gefährdungen für eine bestimmte Maschinenart. Diese können als Gedächtnisstütze dienen, damit nichts Wichtiges übersehen wird.
„Uns ist doch noch nie etwas passiert“ – die trügerische Sicherheit: Manche Unternehmen argumentieren, dass sie seit Jahren Maschinen bauen oder betreiben, ohne je formell eine Risikobeurteilung durchgeführt zu haben, und dennoch sei nichts passiert. Tatsächlich wenden erfahrene Konstrukteure intuitiv viel richtiges Sicherheitswissen an. Aber kann man sicher sein, wirklich alle Risiken bedacht zu haben? Und was, wenn Jahre später doch ein Unfall passiert und man nachweisen muss, welche Überlegungen man damals angestellt hat? Ein systematischer Risikobeurteilungs-Prozess schafft hier Klarheit und Nachvollziehbarkeit. Er dokumentiert die Sicherheitsentscheidungen und sorgt dafür, dass man nicht auf „blinde Flecken“ hereinfällt.
Dokumentationsfalle: Apropos Nachweis – die Dokumentation der Risikobeurteilung ist Pflicht und zugleich ein häufiger Stolperstein. Was gehört alles rein? Mindestens sollten in der Dokumentation folgende Punkte nachvollziehbar enthalten sein:
Beschreibung der Maschine: Was wird beurteilt (Maschinentyp, Modell, Einsatzbereich)?
Relevante Sicherheits- und Gesundheitsschutzanforderungen: Welche gesetzlichen Vorgaben und Normen gelten für diese Maschine?
Identifizierte Gefährdungen: Alle erkannten Gefahrenquellen und Gefährdungssituationen.
Risikominderungs-Maßnahmen: Welche Schritte und technischen/organisatorischen Maßnahmen wurden ergriffen, um die Gefahren zu beseitigen oder Risiken zu reduzieren?
Angewandte Normen und Spezifikationen: Welche Normen wurden herangezogen, um die Schutzziele zu erreichen (z.B. EN ISO 13849 für Steuerungssicherheit)?
Restrisiken: Welche verbleibenden Risiken konnten konstruktiv nicht vollständig beseitigt werden und müssen vom Betreiber beachtet werden?
Diese Dokumentation dient intern als Wissensspeicher und muss auf Verlangen Behörden vorgelegt werden können (z.B. Marktaufsicht oder Berufsgenossenschaften). Kunden bzw. Betreibern muss die komplette Risikobeurteilung zwar nicht ausgehändigt werden – sie enthält ja oft firmenspezifisches Know-how – aber alle sicherheitsrelevanten Informationen daraus müssen in die Betriebsanleitung der Maschine einfließen. So erfährt der Endanwender, welche Restrisiken bestehen und welche Schutzmaßnahmen zu beachten sind.
Ein häufiger Fehler ist, die Risikobeurteilung als lästige Formalität abzutun und erst am Ende eines Projekts „schnell noch“ zu erledigen. Das führt zu lieblosen Copy-Paste-Dokumenten, die im Zweifel an der Realität vorbeigehen. Oder es werden Gefahren nur pro forma erwähnt, aber nicht wirklich behoben. Gerade kleine und mittelständische Unternehmen schrecken manchmal vor dem Aufwand zurück. Dabei sollte die Devise sein: Sicherheit mitdenken, nicht mitschleppen. Wer die Risikobeurteilung proaktiv angeht, spart am Ende Zeit und Kosten – weil teure Nacharbeiten oder Unfälle vermieden werden.
Gegenargumente und alternative Perspektiven
Natürlich gibt es auch Gegenstimmen: „Risikobeurteilung kostet doch nur Zeit und Geld und bremst die Innovation.“ Oder: „Unsere Ingenieure wissen schon, was sie tun – wozu brauchen wir Papierkram?“ Diese Perspektiven sind verständlich, aber sie greifen zu kurz. Sicherheit und Innovation müssen kein Widerspruch sein. Im Gegenteil, eine durchdachte Risikobeurteilung kann Innovation sogar fördern. Wie das? Zum Beispiel indem sie den Entwicklern hilft, kreativere Lösungen zu finden: Eine Maschine, die von Grund auf sicher konstruiert ist, braucht keine klobigen nachträglichen Schutzgitter – sie kann freier und oft auch ergonomischer gestaltet werden.
Ein oft genanntes Gegenargument ist der vermeintlich hohe Aufwand. Ja, eine gründliche Risikobeurteilung erfordert Zeit, interdisziplinäre Zusammenarbeit und Know-how. Aber man sollte sie als Investition sehen: Jeder identifizierte und behobene Risikofaktor ist ein potenzieller verhinderter Unfall. Und Unfälle sind teuer – nicht nur finanziell (Produktionsausfall, Schadenersatz, eventuelle rechtliche Konsequenzen), sondern auch in puncto Reputation und Mitarbeitervertrauen. Eine Rechnung aus der Praxis: Was kostet mehr – ein paar Tage zusätzliche Konstruktionsarbeit oder ein Arbeitsunfall mit Folgekosten in Millionenhöhe? Die Antwort ist klar.
Eine weitere Perspektive: „Wir haben doch schon eine Gefährdungsbeurteilung nach Arbeitsschutzgesetz im Betrieb – reicht das nicht?“ Hier muss man unterscheiden: Die Gefährdungsbeurteilung gemäß Arbeitsschutzgesetz (und Betriebssicherheitsverordnung) ist die Pflicht des Betreibers einer Maschine und bezieht sich auf den konkreten Arbeitsplatz und die Nutzung der Maschine im Betrieb. Die Risikobeurteilung nach Maschinenrichtlinie hingegen ist die Pflicht des Herstellers und betrachtet die Maschine an sich, unabhängig vom Einsatzort. Beide ergänzen einander. Idealerweise übernimmt der Betreiber eine Maschine, die vom Hersteller umfassend bewertet und sicher konstruiert wurde – und ergänzt eigene Maßnahmen für den sicheren Einsatz im Betrieb (z.B. Schulungen, Betriebsanweisungen).
Historische Entwicklung der Risikobeurteilung
Ein kurzer Blick zurück: Arbeitssicherheit im Maschinenbau hat eine lange Geschichte. Im 19. Jahrhundert, zur Zeit der Industrialisierung, waren Maschinen erstmalig große Unfallquellen – Schutzvorrichtungen gab es kaum. Nach und nach entstanden erste Sicherheitsvorschriften, oft als Reaktion auf schwere Unglücke. In Deutschland spielten die Berufsgenossenschaften (BG) schon seit dem frühen 20. Jahrhundert eine wichtige Rolle, indem sie Unfallverhütungsvorschriften erließen. Doch ein systematischer Ansatz zur Risikobewertung etablierte sich erst spät. In den 1970er Jahren entwickelte man in verschiedenen Industriezweigen Methoden wie die FMEA (Fehlermöglichkeits- und Einflussanalyse), um Risiken analytisch zu bewerten.
Der große Umbruch kam mit der europäischen Harmonisierung des Produktrechts. 1989 wurde die erste EU-Maschinenrichtlinie verabschiedet (89/392/EWG), die ab 1995 in den Mitgliedstaaten galt. Sie verlangte schon, dass Maschinen „sicher konstruiert“ sein müssen, und implizit eine Analyse der Gefahren. Allerdings wurde der Begriff Risikobeurteilung erst mit der Neufassung der Maschinenrichtlinie 2006 eindeutig definiert. Diese Richtlinie (2006/42/EG) legte den Grundstein für das heutige Vorgehen und machte die Risikobeurteilung zum zentralen Element der CE-Kennzeichnung. Der vormals verwendete Begriff „Gefahrenanalyse“ wich dem umfassenderen Ansatz der Risikobeurteilung.
Seitdem hat sich viel getan: Normen wie ISO 12100 wurden international abgestimmt, branchenspezifische Standards kamen hinzu, und die Methodik wurde immer weiter verfeinert. Hersteller greifen heute auf einen riesigen Erfahrungsschatz und Hilfsmittel zurück, von Datenbanken mit bekannten Risiken bis zu Software-Tools, die den Prozess unterstützen.
Aktueller Stand und zukünftige Trends
Aktuell (Stand 2025) ist die Risikobeurteilung fest im Maschinenbau-Alltag verankert. Dennoch passieren weiterhin Unfälle mit Maschinen, was zeigt, dass die Aufgabe nie „abgeschlossen“ ist. Laut Statistik der Deutschen Gesetzlichen Unfallversicherung (DGUV) gab es allein im Jahr 2023 23.899 meldepflichtige Arbeitsunfälle im Zusammenhang mit stationären Maschinen, darunter 11 tödliche Unfälle. Jede dieser Zahlen erinnert uns daran, warum wir Risikobeurteilungen brauchen – als Werkzeug, um solche Unfälle in Zukunft zu verhindern.
Ein aktuelles Stichwort ist die Manipulationssicherheit: Wie verhindert man, dass Bediener Schutzeinrichtungen absichtlich manipulieren (z.B. Türen überbrücken), um schneller arbeiten zu können? Die DGUV Information 209-092 widmet sich diesem Thema und gibt Tipps, wie Konstrukteure Schutzmaßnahmen manipulationssicher gestalten können (z.B. durch verriegelte Türen, die sich nur im Stillstand öffnen lassen). Hier zeigt sich ein Trend: Risikobeurteilung endet nicht bei „Schutz dran und gut“, sondern bezieht menschliches Verhalten mit ein.
Digitalisierung und Industrie 4.0 beeinflussen ebenfalls die Risikobeurteilung. Immer mehr Hersteller setzen Software ein, um den Prozess zu strukturieren. Spezialisierte Tools erleichtern z.B. das Dokumentieren erheblich – per Eingabeassistent und Vorlagen entsteht der Bericht fast nebenbei. Auch komplexe Berechnungen, etwa für funktionale Sicherheit (Stichwort Performance Level (PL) / SIL), lassen sich mit Tools wie SISTEMA der DGUV unterstützen. Die Digitalisierung geht aber noch weiter: In Zukunft könnte man Risikosimulationen am digitalen Zwilling einer Maschine durchführen, bevor überhaupt ein Prototyp gebaut wird. KI-basierte Systeme könnten Konstrukteure auf „vergessene“ Gefahren hinweisen, indem sie aus einer Fülle von bestehenden Risikodaten lernen.
Apropos KI: Die nächste Generation der Maschinenrichtlinie steht bereits in den Startlöchern – oder besser gesagt, eine Maschinenverordnung. Die Verordnung (EU) 2023/1230 wurde 2023 verabschiedet und wird ab dem 20. Januar 2027 verbindlich gelten. Sie löst die bisherige Richtlinie ab und passt das Regelwerk an neue technologische Entwicklungen an. Ein besonderer Fokus der neuen EU-Maschinenverordnung liegt auf digitalen und KI-gestützten Maschinen sowie autonomen Systemen, die im aktuellen Normenwerk noch nicht ausreichend abgebildet sind. Das bedeutet, es werden klarere Anforderungen an Maschinen mit Künstlicher Intelligenz kommen – etwa an kollaborative Roboter, die ohne Schutzzäune neben Menschen arbeiten. Für die Risikobeurteilung heißt das: Hersteller müssen künftig auch Risiken durch Software, Vernetzung und KI-Entscheidungen bewerten. Eine spannende Herausforderung, denn wie beurteilt man z.B. das Risiko, dass ein lernfähiger Algorithmus in einer Maschine falsche Entscheidungen trifft? Hierzu laufen bereits Forschungsprojekte, und Normungsgremien arbeiten an Leitfäden.
Ein weiterer Zukunftstrend ist die Modularisierung von Risikobeurteilungen. Große Anlagen könnten in Modulen beurteilt werden, die dann zusammengesetzt ein Gesamtbild ergeben – ähnlich wie Softwaremodule, die man verifiziert und dann integriert. Zudem gewinnt das Thema Usability und Ergonomie an Bedeutung: Maschinen sollen nicht nur technisch sicher sein, sondern auch fehlbedienungssicher – also so gestaltet, dass Anwender gar nicht erst in Versuchung kommen, unsicher zu handeln.
Wann lohnt sich externe Unterstützung?
Angesichts all dieser Anforderungen fragen sich viele Unternehmen: „Können wir das alleine stemmen, oder brauchen wir Unterstützung?“ Gerade kleinere Hersteller oder Betriebe ohne eigene CE-Abteilung profitieren oft von externer Expertise. Ein Ingenieurbüro wie NEERTEX hat Erfahrung aus diversen Projekten und kennt die Fallstricke – es weiß, wo man genauer hinschauen muss und welche Normen aktuell relevant sind. Das spart Zeit und Nerven. Insbesondere in folgenden Situationen lohnt es sich, über externe Unterstützung nachzudenken:
Neuentwicklung einer komplexen Maschine oder Anlage: Bei innovativen Technologien gibt es vielleicht noch keine firmeneigenen Erfahrungswerte. Externe Experten bringen das nötige Fachwissen mit und sorgen dafür, dass nichts übersehen wird.
Umrüstung oder Erweiterung bestehender Anlagen: Wenn bestehende Maschinen modifiziert oder zu einer Anlage verkettet werden, wird die Risikobeurteilung schnell kompliziert. Hier helfen externe Spezialisten, die Gesamtsicherheit im Blick zu behalten und alle Schnittstellen zu bewerten.
Engpässe in der Manpower: Die beste Risikobeurteilung nützt nichts, wenn sie aus Zeitmangel liegenbleibt. Wer wichtige Deadlines einhalten muss (Produktlaunch, Kundentermine), kann mit externen Dienstleistern die Risikobeurteilung parallel vorantreiben lassen.
Dokumentation und Behördenkommunikation: Manche Unternehmen tun sich schwer, die Ergebnisse verständlich zu dokumentieren oder im Fall der Fälle mit Behörden zu kommunizieren. Experten kennen die Anforderungen und formulieren die Dokumentation so, dass sie den offiziellen Erwartungen entspricht.
Eine Zusammenarbeit mit externen Partnern heißt nicht, die Verantwortung abzugeben – der Hersteller bleibt verantwortlich. Aber es heißt, sich zusätzliche Sicherheit zu holen. Externe sehen oft den Wald trotz lauter Bäume: Sie erkennen Risiken, die betriebsblinde interne Teams vielleicht übersehen. Außerdem bringen sie Best Practices mit. So wird die Risikobeurteilung nicht nur zum Pflichtübung, sondern kann auch zu einem Lernprozess für das interne Team werden. Man wächst an den Fragen der Experten und versteht am Ende die eigene Maschine noch besser.
Fazit: Sicherheit zahlt sich aus
Die Risikobeurteilung für Maschinen und Anlagen mag auf den ersten Blick wie viel Aufwand klingen, doch sie ist weit mehr als bürokratische Pflicht. Sie ist das Sicherheitsnetz unter dem Hochseil der Innovation – sie fängt uns auf, wenn wir etwas übersehen haben, und erlaubt uns gleichzeitig, waghalsigere Kunststücke zu wagen, weil wir wissen, dass das Netz trägt. Historisch hat sich gezeigt, dass systematische Risikoanalysen Maschinen sicherer gemacht haben. Aktuell ist die Risikobeurteilung integraler Bestandteil jedes Entwicklungsprojekts, und in Zukunft wird sie sich an neue Technologien anpassen und diese sicher nutzbar machen.
Unternehmen, die die Risikobeurteilung ernst nehmen, profitieren mehrfach: Sie vermeiden Unfälle, Ausfallzeiten und Haftungsprobleme, sie erfüllen ihre gesetzlichen Pflichten nach Maschinenrichtlinie ohne Bauchschmerzen, und sie gewinnen das Vertrauen ihrer Mitarbeiter und Kunden. Denn nichts zeigt Verantwortungsbewusstsein so deutlich wie eine Maschine, der man ansieht, dass an jede Sicherheitsschraube gedacht wurde.
Zum Schluss ein hypothetisches Szenario, das niemand erleben will: Stellen Sie sich vor, es kommt zu einem schweren Unfall mit einer Ihrer Maschinen. Ermittler fragen nach der Dokumentation der Risikobeurteilung – und es gibt nichts Vorzeigbares. Die Konsequenzen wären fatal, von Produktionsstopps über juristische Maßnahmen bis zum Imageverlust. Zum Glück lässt sich dieses Szenario verhindern. Mit einer gründlichen Risikobeurteilung von Anfang an legen Sie den Grundstein dafür, dass Ihre Maschinen sicher und erfolgreich betrieben werden können.
NEERTEX steht Ihnen dabei gerne als Partner zur Seite – mit Erfahrung, Fachwissen und Leidenschaft für sichere Technik. Machen Sie die Risikobeurteilung nicht nur zur Pflichterfüllung, sondern zur Chance, Ihre Maschinen und Anlagen noch besser zu machen. Sicherheit zahlt sich aus – für Ihr Unternehmen und für alle, die tagtäglich mit Ihren Maschinen arbeiten.
Quellen: Die in diesem Beitrag genannten Fakten und Zitate stammen aus offiziellen Quellen wie der EU-Maschinenrichtlinie, Veröffentlichungen der Bundesanstalt für Arbeitsschutz und namhaften Fachpublikationen. Beispielsweise betont die DGUV die Pflicht zur Risikobeurteilung als Grundlage jeder CE-Kennzeichnung, und die BAuA stellt klar, dass es sich um eine gesetzliche Anforderung handelt. Weiterführende Informationen finden Sie u.a. bei TÜV Süd zum Thema „Risikobeurteilung nach Maschinenrichtlinie“, im Leitfaden zur Anwendung der Maschinenrichtlinie 2006/42/EG sowie in Forschungsergebnissen zur praktischen Umsetzung der Risikobeurteilung im Maschinenbau. Die Statistik zu Arbeitsunfällen mit Maschinen wurde der DGUV-Unfallstatistik 2023 entnommen.
Individuelle Beratung
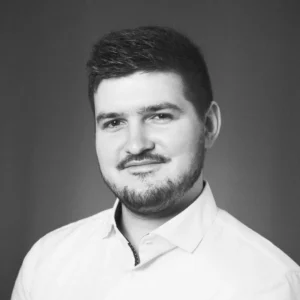
Malte Güttner
Maschinenbauingenieur (M.Eng.)